
Question sent by email:
I've heard you say you can save 40% of domestic water without any added cost. How do you do this? Is it use of gray water for flushing in addition to waterless urinals, low flow toilets, aerators on sinks, etc???
Response:
It was very easy to do in the past with fixture selection. The water efficient fixtures we use have no added cost compared to conventional fixtures. We could save a tiny bit more with gravity fed toilets (the kind with the tank like you have at home), but we usually use flushometer toilets (the more commercial kind with the silver pipes sticking out of the wall).
Lets look at the calculations assuming there are two people in the building, one man and one woman.
Base Case (code compliant)
Toilet = 1.6 gpf - 3 times/day for woman, 1 time for man
Urinal = 1.0 gpf - 0 times/day for woman, 2 times for man
Sink = 2.5 gpm @ 80 psi - 3 times/day for 25 seconds for everybody
Shower = 2.5 gpm @ 80 psi - 1 times/day for 5 minutes for 10% of people
Design Case (what we do)
Toilet = 1.6 / 1.1 gpf dual flush - 1 full 2 half times/day for woman, 1 full for man
Urinal = 0 gpf - 0 times/day for woman, 2 times for man
Sink = 0.5 gpm @ 80 psi - 3 times/day for 20 seconds (sensors) for everybody
Shower = 1.6 gpm @ 80 psi - 1 time/day for 5 minutes for 10% of people
The scenario above would save 48.1% of the water in an office setting based on a comparison to EPAct 1992 (calculation for LEED NC v2.2):

Now we usually get a little less credit for the same water usage because the base case for commercial sinks has been reduced to 0.5 gpm @ 60 psi.
Base Case (code compliant)
Toilet = 1.6 gpf - 3 times/day for woman, 1 time for man
Urinal = 1.0 gpf - 0 times/day for woman, 2 times for man
Sink = 0.5 gpm @ 60 psi - 3 times/day for 25 seconds for everybody
Shower = 2.5 gpm @ 80 psi - 1 times/day for 5 minutes for 10% of people
Design Case (what we do)
Toilet = 1.6 / 1.1 gpf dual flush - 1 full 2 half times/day for woman, 1 full for man
Urinal = 0 gpf - 0 times/day for woman, 2 times for man
Sink = 0.5 gpm @ 80 psi - 3 times/day for 20 seconds (sensors) for everybody
Shower = 1.6 gpm @ 80 psi - 1 time/day for 5 minutes for 10% of people
The scenario above would save 34.8% of the water in an office setting based on a comparison to EPAct 1992 and the new commercial fixture rules (calculation for LEED 2009). Of course there is no kitchen sink in this example (assuming a college dorm), but that would have to be added in if appropriate:
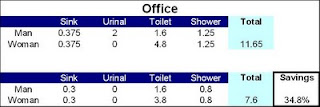
Residential buildings code still allows 2.5 gpm sinks, so we typically save 38.1% in old and new versions of LEED.
Base Case (code compliant)
Toilet = 1.6 gpf - 5 flushes/day for all
Sink = 0.5 gpm @ 60 psi - 5 times/day for 25 seconds
Shower = 2.5 gpm @ 80 psi - 1 time/day for 5 minutes
Design Case (what we do)
Toilet = 1.6 / 1.1 gpf dual flush - 1 full & 4 half flushes/day for all
Sink = 0.5 gpm @ 80 psi - 5 times/day for 25 seconds
Shower = 1.6 gpm @ 80 psi - 1 times/day for 5 minutes

Of course the calculations above are done for 2 people, but the percent reduction will remain the same regardless of the number of people as long as you assume a 50/50 split between men and women.
We have plans to use greywater in some buildings and one of my projects in South Carolina did this (see Half Moon Outfitters case study). Showers really drive the numbers in residential buildings and it is possible to go below 1.6 gpm. We usually use Delta H20 Kinetic showers, but many of the best low-flow showers aren't allowed in Massachusetts because they're not on the approved plu
mbing list. The toilet in the top right is a tank-type dual flush from Dubai. The urinal on the bottom left uses no water for flushing and has a trap that can be cleaned and refilled with oil (Kohler Steward).
Hope this helps.